Top 6 warehousing mistakes to avoid
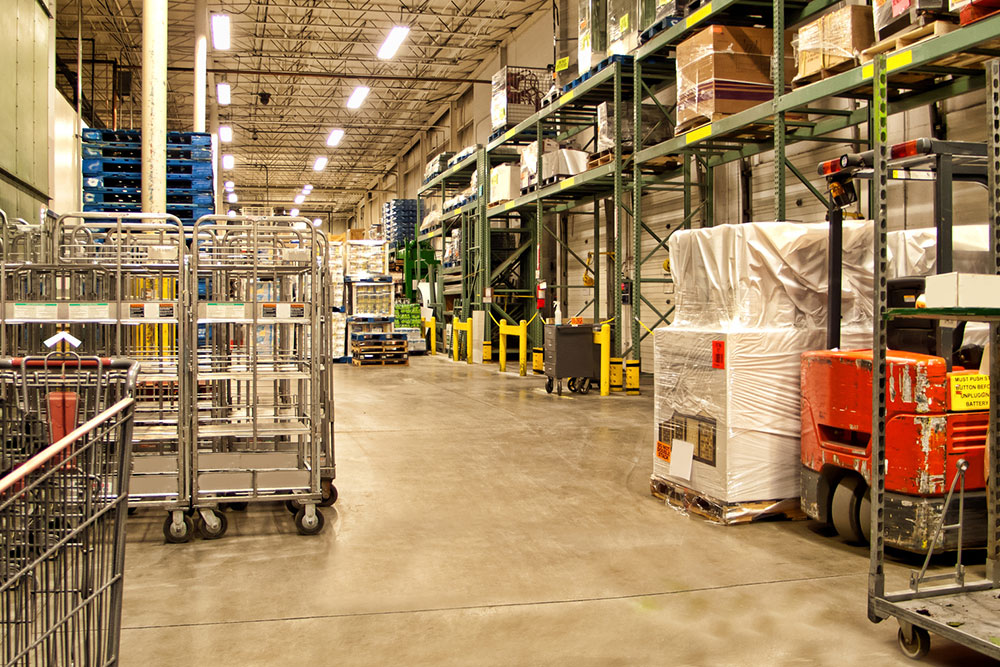
With the growth of mass production and the advent of online ordering, supply chain management has become more complex than ever. It has also made customers expect rapid product delivery. As a result, warehouses have become the backbone of many businesses. Good warehouse management can help businesses fulfill orders with overwhelming accuracy and a short turnaround time. So, to ensure seamless business functioning, streamlining the warehousing process and ironing out any bottlenecks is important.
1. Poor planning
Planning is a non-negotiable part of running a business. One of the biggest mistakes companies make here is not taking this step seriously or following age-old practices that could be slowing the business down. To avoid this, companies must focus their efforts on ensuring that all processes are updated regularly. To do so, they can set up a schedule to meet with stakeholders once or twice a year at least to discuss what competitors are doing, evaluate current processes, and lay down the foundation for new, more efficient warehouse operations.
2. Lapses in inventory tracking
Another common mistake warehouses make is keeping an inaccurate record of inventory or not keeping one at all. This could result in major losses for the business! One can steer clear of this issue by implementing a warehouse management system (WMS) at the location. This is software that can easily update and keep track of tasks like inventory management, order fulfillment, shipping, receiving, reverse logistics, and more.
3. Lack of safety
Amidst all that stock, many businesses forget to prioritize worker safety in the warehouse, resulting in accidents and OSHA lawsuits. This can be avoided by ensuring that the business follows all the recommended health and safety guidelines and has special provisions in place to ensure employee health and safety in the warehouse.
4. No staff training
Given the fast-paced nature of work, it can be difficult to allocate some time for training new joiners. Despite the hassle, companies must ensure that they do not miss this step. One of the biggest positives of training the staff is that it shows them that the company cares. This reduces employee turnover. Moreover, allowing untrained staff on the warehouse floor can increase the risk of accidents and injuries. As they are unaware of the processes, it could also slow down the cycle and compromise team productivity.
5. Dirty facilities
Cleanliness has to be a priority for all warehouses. A space that is dusty, dirty, or has broken remnants of old machines and equipment not only poses a high risk of injuries but also illnesses. Maintaining cleanliness should be a regular chore. So, all parts of the warehouse should be cleaned after every shift. Setting up a deep cleaning schedule can help businesses maintain their warehouses better.
6. Keeping excess inventory
Old stock could be taking up precious space in the warehouse, resulting in a lot of clutter. As these products haven’t been sold for a while, they are likely to expire or go out of style, causing them to go to waste. For effective warehouse management, it is best to let go of excess inventory as much as possible. Additionally, businesses must set up a batch framework for orders so the warehouse can comfortably house items without overflowing.